FUJIFILM
FUJIFILM Achieves 80% Reduction in SAP Testing Time and Accelerates
Service Pack Implementation by 25%
About
FUJIFILM Diosynth Biotechnologies
FUJIFILM Diosynth Biotechnologies (FFDB) is a dedicated biopharmaceutical CDMO business with development and manufacturing sites in Billingham, UK and Research Triangle Park, NC, and College Station, TX, employing over 1,000 people. They have over 30 years of clinical and commercial experience in biopharmaceutical development and cGMP manufacturing.
The Challenge
FUJIFILM Diosynth Biotechnologies (FFDB), the drug contract manufacturing division of FUJIFILM, were upgrading their SAP ERP service packs every 12-18
months. The number of patches contained within each service pack meant it was impractical to manually check each patch for impact, but they had to minimize the risk to business continuity and the systems downtime.
Furthermore, FFDB needed to fit their service pack updates and their test cycle into the timeslots made available by their manufacturing department and ensure that any changes in the development and test environments were carried through to the production system without excessive delays.
They had reduced their tests down to their key processes and processes steps and had created a number of end to end tests but the lapsed time between applying the service packs in the development system and production was still too great and they were still not sure if they were tackling the right tests.
The Solution
The Results
FFDB started to realize the benefits from day one, from faster test creation and execution to increased end user involvement. “This is not only a big time saving, but the test executioner no longer dreads the more complex end to end testing which would have upwards of 50 screen captures,” stated Verrill. “We’ve taken a month off of service pack implementation quite easily.” said Kay.
In an article in Computerworld UK, Kay states that Panaya automates the test execution process, capturing and recording test steps and data with
the press of a button, saving FDDB 80% of time it used to spend on testing. In addition, automating this process has helped FFDB to implement service packs between 20% and 25% faster, Kay said.
Using Panaya proved to deliver change better, faster and safer, ensuring that FFDB’s SAP landscape meets the rising demands and pace of today’s business.
Our Latest
Resources
Guide
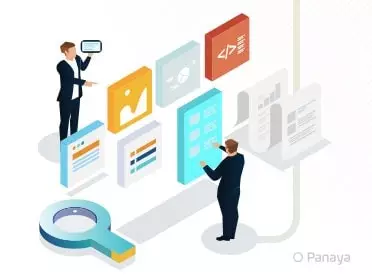
Greenfield Acceleration, Minus the Risk
Webinar On-Demand
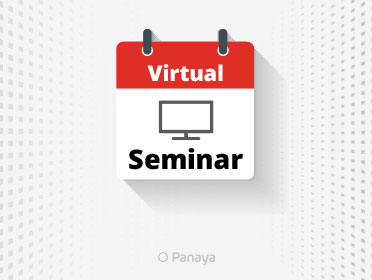
Tips and Tricks for Successful UAT
Datasheet
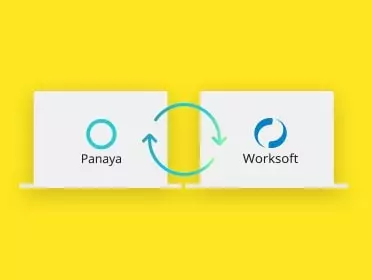
Panaya Test Dynamix – Worksoft Integration